
Corrugated Cardboard Production Line
2025 year Beckhoff Fully Automatic 5Ply Corrugated Cardboard Production Line
Fully Automatic Whole Carton Plant Design Solution from Corrugated to printing, flat die cutting, fold gluing, full factory conveying system of paper roll and cardboard, finished machines....
Latest production line adopts West River self-developed BECKHOFF control system for Industry 4.0. It replaces the traditional control of more than ten distributed PLCs with two high-performance controllers, one for control and the another for backup data. Its biggest advantage is that it can achieve efficient centralized processing of information. Compared with the PLC control currently used by most manufacturers, it is like a computer controlling more than ten machines at the same time, and more than ten Nokia controllers controlling more than ten machines. Refined data feedback processing and centralized processing, efficient and timely processing of feedback information from different devices, improving the automation control of the production line, reducing reliance on the experience of operators, and achieving foolproof operation. Simultaneously reducing losses caused by human factors and quality issues in cardboard production, achieving efficient and high-quality cardboard output.
This system, combined with West River's latest fully digital control method, achieves temperature, glue, tension, gap, the fully digital control scheme for pressure has upgraded the laser ranging function, achieving precise adjustment of paper and speed according to different production orders. At the same time, with the help of a self-learning system, it can continuously learn and optimize through big data models, reducing the quality problems caused by human experience in cardboard.
This system also integrates the PMS production management system of WEST RIVER, achieving precise automation adjustment for different types of paper, cardboard, corrugated shapes, production speeds, and other situations. It manages and produces statistics for different customers and orders, and combines different orders to achieve efficient production.
This system adopts both fiber optic data communication in the wet and dry end sections and fiber optic communication in the ring network, which can prevent interference in the long production line caused by traditional PLC analog communication, even in dry conditions such as deserts. The system comes with a regular maintenance function, which regularly reminds operators to maintain and perform equipment maintenance. In the future, with the accumulation of big datas, the system can also upgrade like Windows, just like upgrading from Windows 10 to Windows 11.
At the same time, it is equipped with a remote maintenance system, and our engineers in China can also monitor the operation of each device in real time through this control system.
This production line adopts our company's brand new European version design and appearance, as well as the European CE mechanical and electrical control safety standards. CE's electrical control cabinet and aviation plug are installed and debugged quickly at customer's site.
In response to the current demand for multiple orders per day from customers in the market, with over 600 orders, we have equipped two of our company's most advanced Single Facer machines with 5-minutes quickest flute change. Compared with the normal cassette type Single Facer on the market which takes at least 15 minutes to remove the corrugated roller from the inside and replace it with a new corrugated roller, and takes about 30 minutes after preheat and machine. The fast change Single Facer can achieve true 5-minute corrugated roller replacement, adopting a fully hydraulic control integrated dual station design. Before replacement, the other pair of corrugated rollers can be preheated in advance and only takes 5 minutes to complete the replacement operation through hydraulic control, which can greatly improve production efficiency in multiple order states.
At the same time, the corrugated line adopted the design of a dual slitter scorers machine and a multi-functional shearer machine, which, under the control of the PMS system and in conjunction with the WEST RIVER BECKHOFF control system, enables rapid order replacement of Dry End, achieving efficient and non-stop replacement of 600-900 orders per day. The latest developed cardboard unloading system is also used for large stack output, achieving efficient cardboard unloading and production. PMS enables label printing of orders, thus achieving fully digital order factory management.
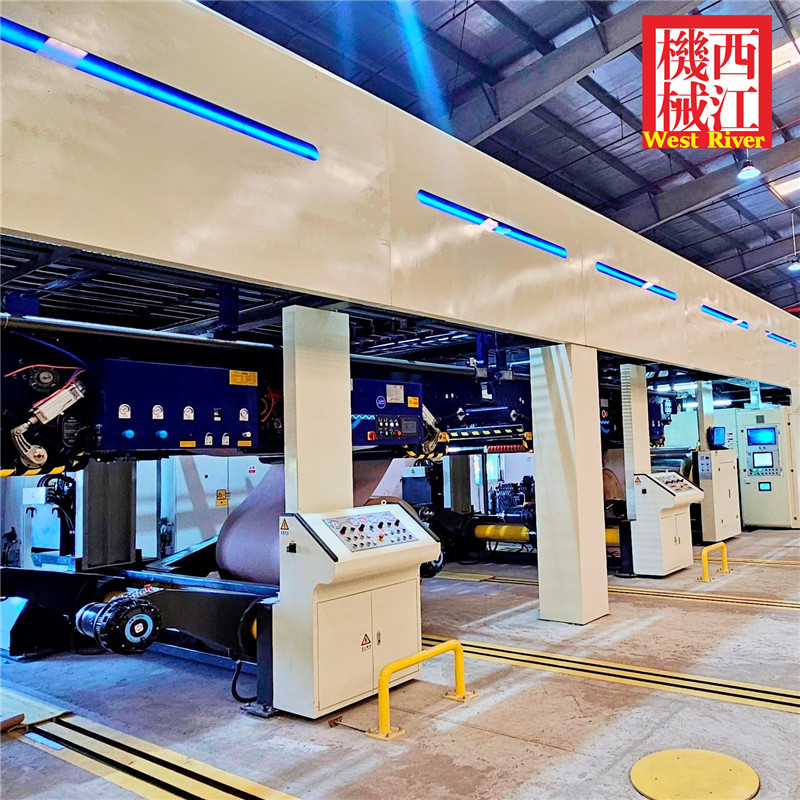
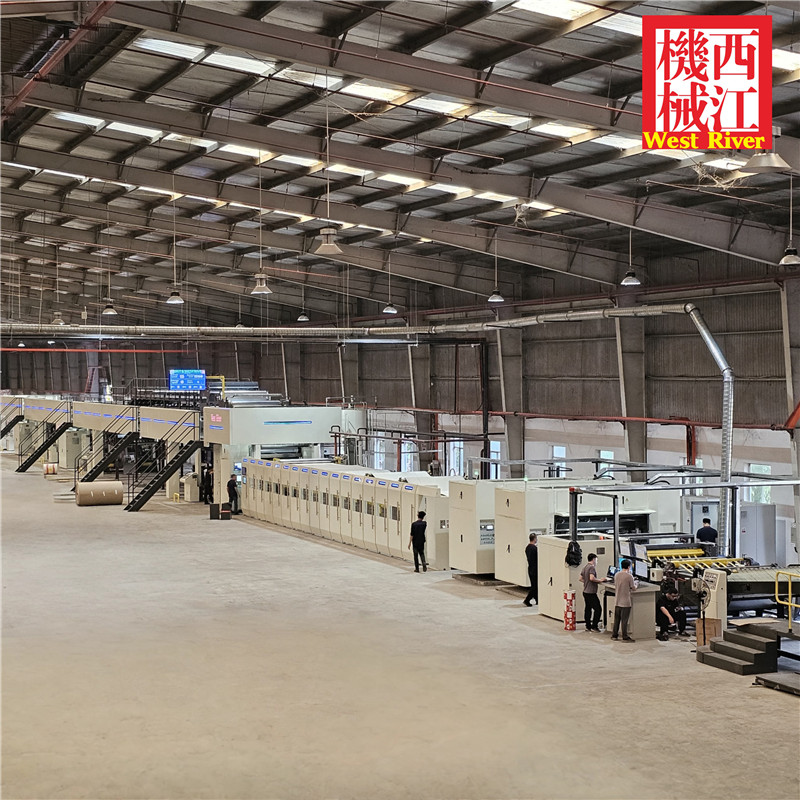

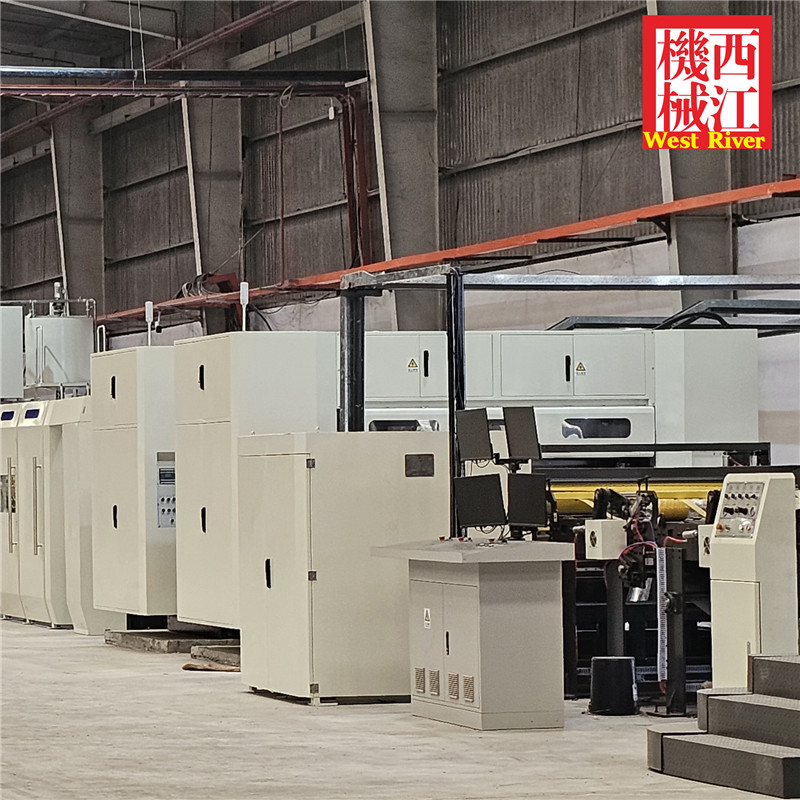
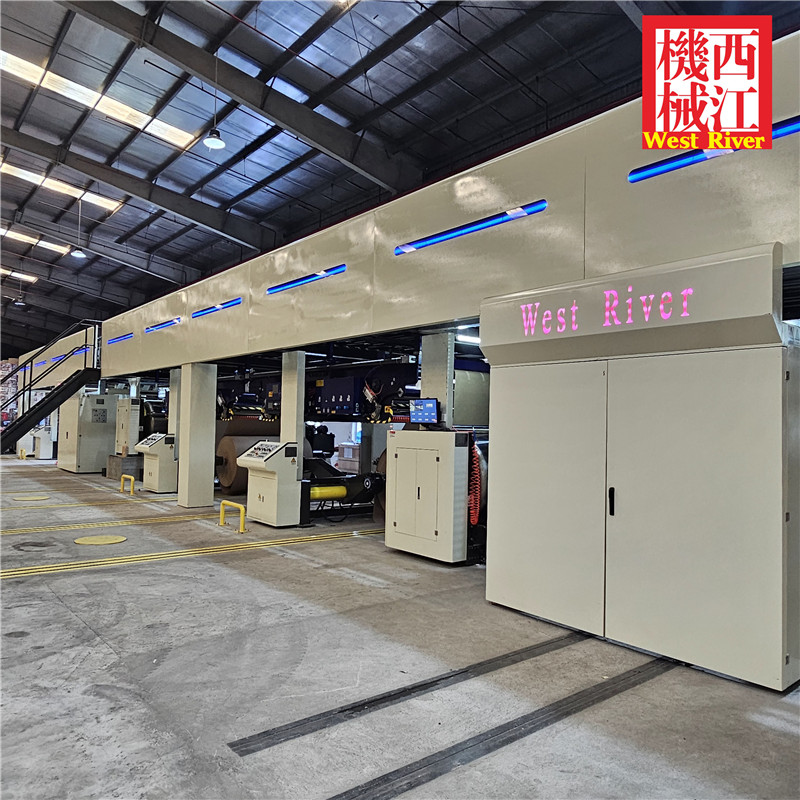
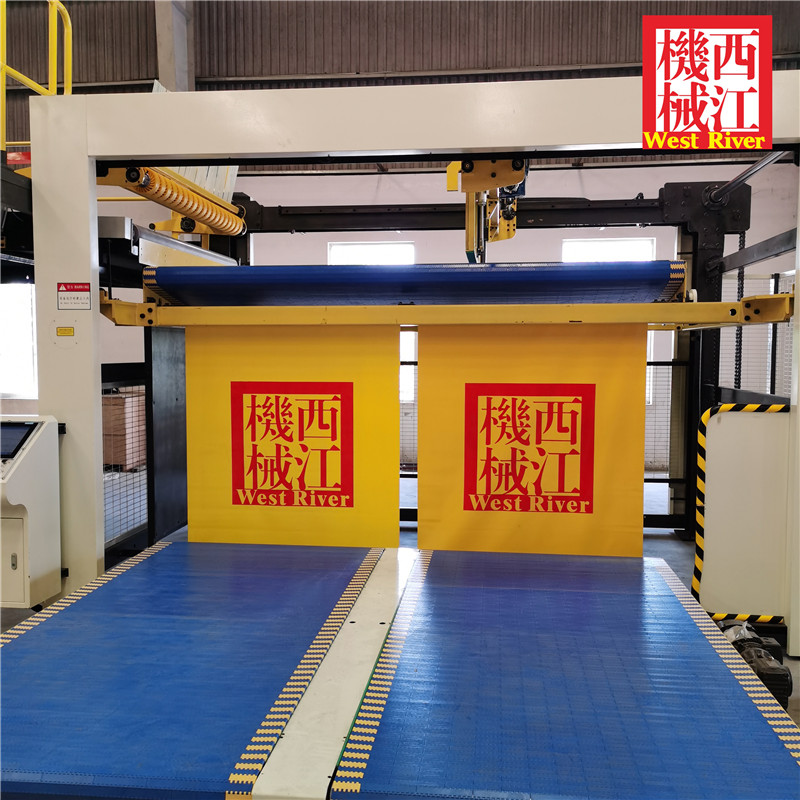
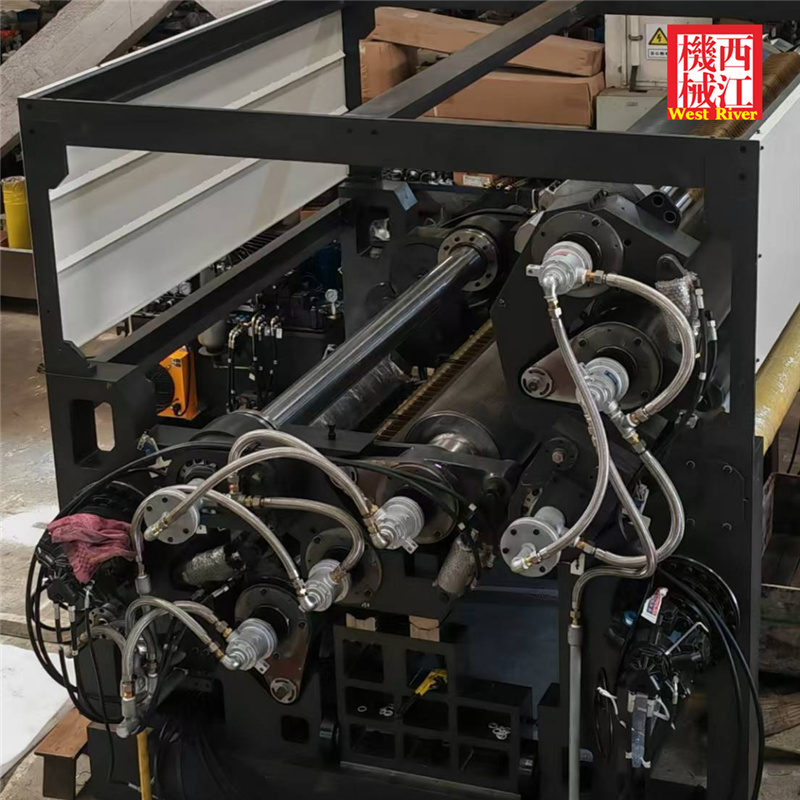